Cleaning Metal Stampings Is Critical to Its Finish and Function
- Nico Cottone
- Nov 29, 2022
- 3 min read
Having a surface that is properly cleaned and polished is a crucial factor in the performance and longevity of metal stampings. It's a process that involves a number of steps, including surface hardness testing, aqueous degreasing, vibrational deburring and passivation.
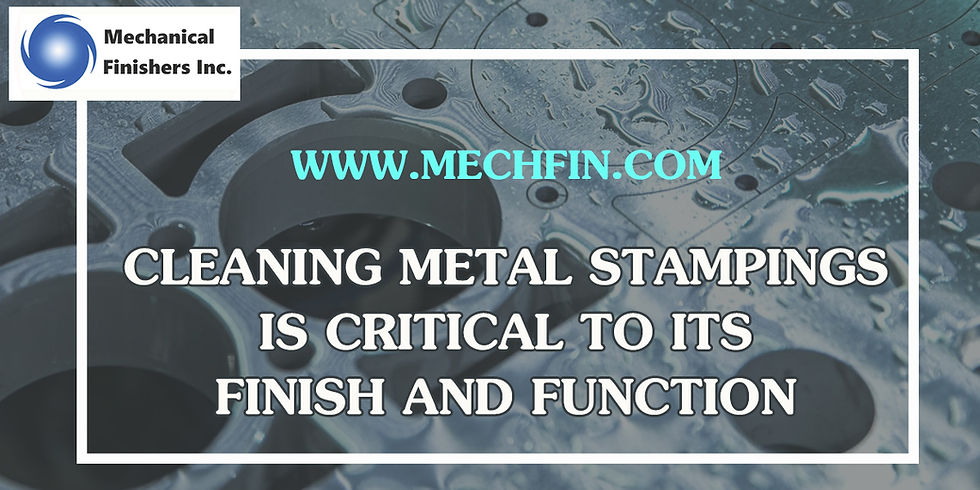
Aqueous Degreasing
During the production of metal stamping parts, aqueous degreasing is essential. This process emulsifies stamping fluids and other contaminants that affect the finish and function of the parts. The contaminants can include greases, oxides, and buff compounds. The process requires the use of high-pressure pumps and other equipment to prepare the parts for cleaning. In addition, it requires energy to heat the cleaning water, pre-treat the parts, and dry them. The quality of the finished parts is dependent on the cleaning process and the number of rinsing baths used. To help determine which metal cleaner to use, the contaminant's polarity and solubility must be known. Information about the contaminant is also used to choose the appropriate equipment for a particular cleaning application. In addition to solvents, aqueous cleaning systems are also used to remove oily contaminants. These systems are commonly used to clean castings and other metal parts that have neat oils. The aqueous cleaning solution is usually diluted with water, but may be formulated with other chemicals.
Vibratory Deburring
During the manufacturing process, vibratory metal deburring is a critical process to ensure the finish and function of the part. This process removes raised edges and burrs from the surface of metal parts, resulting in a polished, smooth and uniform surface. The vibratory deburring of metal stamping process combines a variety of techniques. It is a batch-type operation that uses specially-shaped pellets of media. This media carries abrasive particles and other elements. The media mass moves in a counter-clockwise direction during the deburring process.
The media mass also helps compounds perform their cleaning functions. The mass is made up of a wide variety of materials, including steel, ceramics, slag, and synthetics. Media are used for both light and heavy deburring applications. In the vibratory deburring of metal stampings, parts are tumbled in an abrasive media. These media are used to smooth and deburr parts, and to remove dust. The process is particularly effective for delicate parts and large surfaces.
Passivation
Stainless steel stampings are a critical part of any manufacturing process. In addition to being able to meet the necessary specifications for their application, they must also be free of rusting, and clean. These requirements are met through a process called passivation. Passivation involves the immersion of metal parts in a chemical bath. This removes any free iron that has been deposited on the surface, as well as any other contaminants that may have been present during forming or processing. The process also creates a protective "passive" layer on the surface of the part, which enhances its corrosion resistance.
Also read for, Beginners Guide To Mass Finishing
There are a variety of passivation techniques available. Each technique has its own benefits and disadvantages. Choosing the right passivation process for your application depends on the product grade, the industry, and your customer's needs. During the passivation process, the chromium in the material is changed to chromium oxide, which protects the underlying iron from rusting. The oxide film also enhances sterilization.
Surface Hardness
Whether it's a new part or an old one, metal stampings need to be cleaned prior to being put through various other processes. The type of cleaning process that's used is a factor in determining how the part will perform. The quality of the finished part is also impacted by the cleaning process.
Various metal stamping cleaning processes include degreasing, vapor degreasing, and aqueous degreasing. Each of these processes is suitable for cleaning stamped parts with water-soluble lubricants. Aqueous degreasing may be performed by in-line spraying parts in a water-based cleaner.Surface treatments increase tool life and reduce friction. These coatings include titanium aluminum nitride (TiAlN), titanium carbide (TiC), and chromium oxide (CrO). Chrome plating and nitriding are also common.
Surface treatments affect tool wear, surface finish, and adhesive wear. The degree of wear depends on the type of material, the tooling, and the sliding contact between the tooling and the material. Optimal surface treatments minimize wear and adhesive wear, reduce rework, and minimize galling.
Selecting the right metal cleaning services cincinnati requires an understanding of the type of metal material, the strength or fragility of the stamping, its size, the level of cleanliness required, and the type of metal finishing that will follow stamping. We provide the best mechanical finishing services then call us these days on +1-513-641-5419 or e-mail info@mechfin.com
Reference Url, https://bit.ly/3XAX7I9
Comments